Met meer dan 100 jaar toegewijd aan technische vooruitgang zijn wij een toonaangevende fabrikant op het gebied van frequentieregelaars, servoaandrijvingen, besturingstechnologie en robotica.
Force Sensor MotoFit
Force Control Assembly Tool
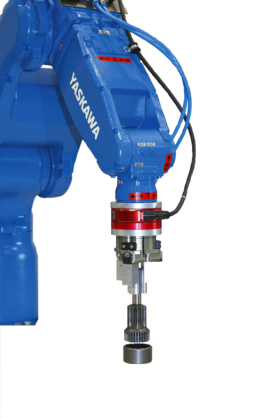
MotoFit alters the robot’s position based on the force encountered to align or assemble parts. (During normal robot operation, the robot is setup for positional control. It moves to or retains position even when external forces are applied, provided that forces do not exceed limits that would cause an error.)
The six-axis force sensor detects three translational forces and three axial moments to detect external forces during job execution. Three operations (touching, fitting and inserting) are combined to provide automatic precision fits of mating surfaces of 10 –100 μm. High speed fits up to 20 mm deep with h7/H7 tolerance can typically be done in five seconds. Also the force sensing control parameters can be taught quickly without unique skills. Its hole position detection and snag prevention increase reliability.
The Engineering Support Tool (EST), a PC application, is used for sensor setup and job creation. It supports one or two robots, up to 24 force files, and robot or tool coordinate systems. Therefore jobs can be edited on the contoller if needed.
Components
• Six-axis sensor (200 N (V) or 1000 N (H or V)
• High-speed communication board
• Power supply box
• Robot-specific mounting flange adapter
• Engineering Support Tool software with interface panel software
- Ability to enable or disable each translational force or axial moment
- Helpful graphics for troubleshooting and setup
- Step-by-step instructions
- Ideal for precision part assembly applications including drive train components, seats, electronics, battery assembly and nondestructive testing