Met meer dan 100 jaar toegewijd aan technische vooruitgang zijn wij een toonaangevende fabrikant op het gebied van frequentieregelaars, servoaandrijvingen, besturingstechnologie en robotica.
In-cell value
A periodic and prudent modernization of production technologies is a fundamental investment for a company. This is well demonstrated by the case of the induction braze welding cell developed for Torneria Castiglioni - an important company in Mantua that has been operating for about thirty years in the precision mechanics sector: a compact, versatile solution capable of guaranteeing important returns from the moment of purchase.
- Industrieën
- Metaalbewerking
- Klant
- Torneria Castiglioni
Challenge
The new induction braze welding cell is intended to contribute not only to automate the production process, but also to optimize production times, allowing an efficient management of both the processing of items in large series and the development of customized solutions.
Solution
At the heart of the cell is a Motoman GP25 6-axis anthropomorphic robot, equipped with a double induction braze welding head powered by a CEIA induction generator. This solution means that the piece to be welded can be handled in a single operation even if 2 different types of welding are required, without having to be reworked several times. The use of a single robot with two welding heads instead of two separate robots also creates immediate efficiencies in terms of both purchase and management costs.
The cell has also been equipped with a double welding station, so as to be able to carry out pendulated machining that allows to manage the loading/unloading activities of the parts in masked time, almost totally eliminating the stops linked to these phases. Productivity is thus continuous, with machining times practically halved.
Results
In addition to the reduction in downtime, the new cell is also distinguished by a considerable reduction in overall dimensions. The Motoman GP25 robot represents the ideal combination of compactness, speed and precision: the slim design of the arm has made it possible to place the robot close to workpieces and minimize interference with peripheral devices, and the YRC1000 control guarantees high trajectory accuracy and high efficiency in a footprint of only 125 litres.
The result is a complete, compact and forcollable monocoque cell.
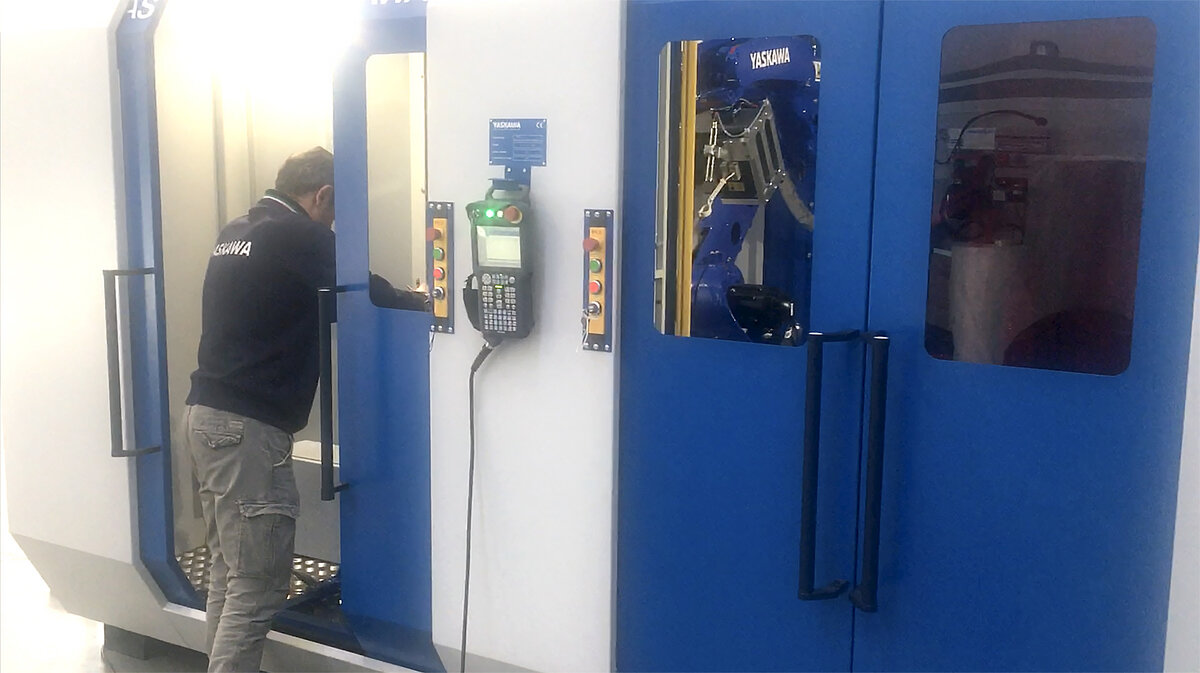
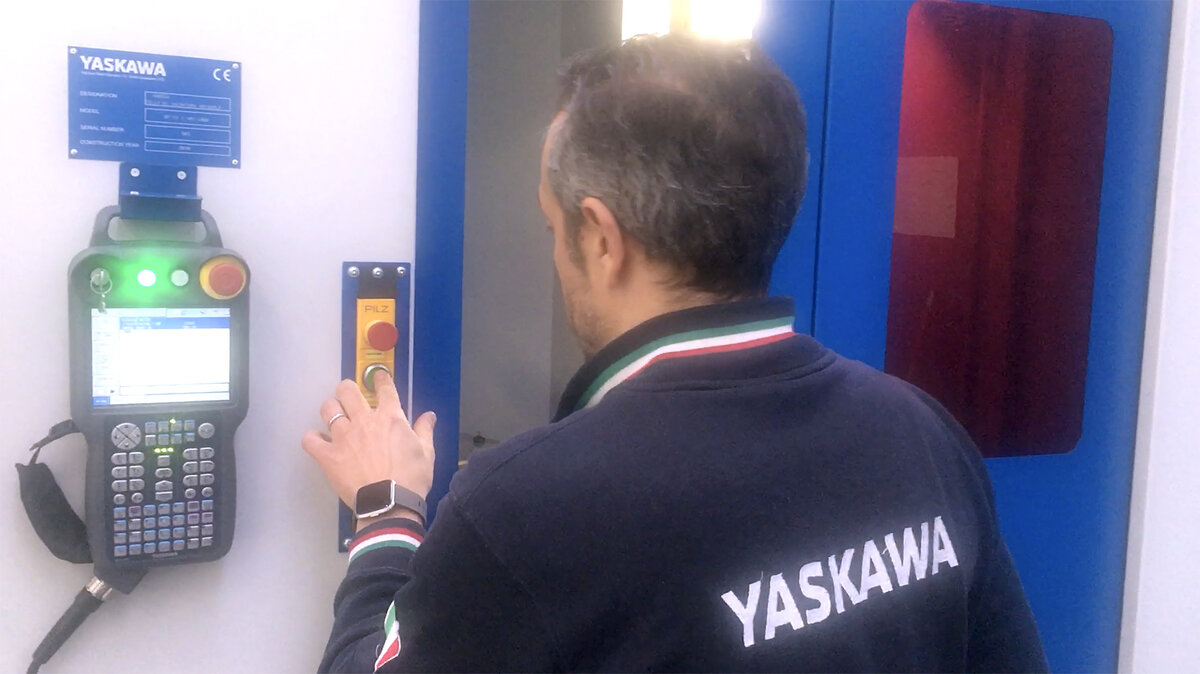
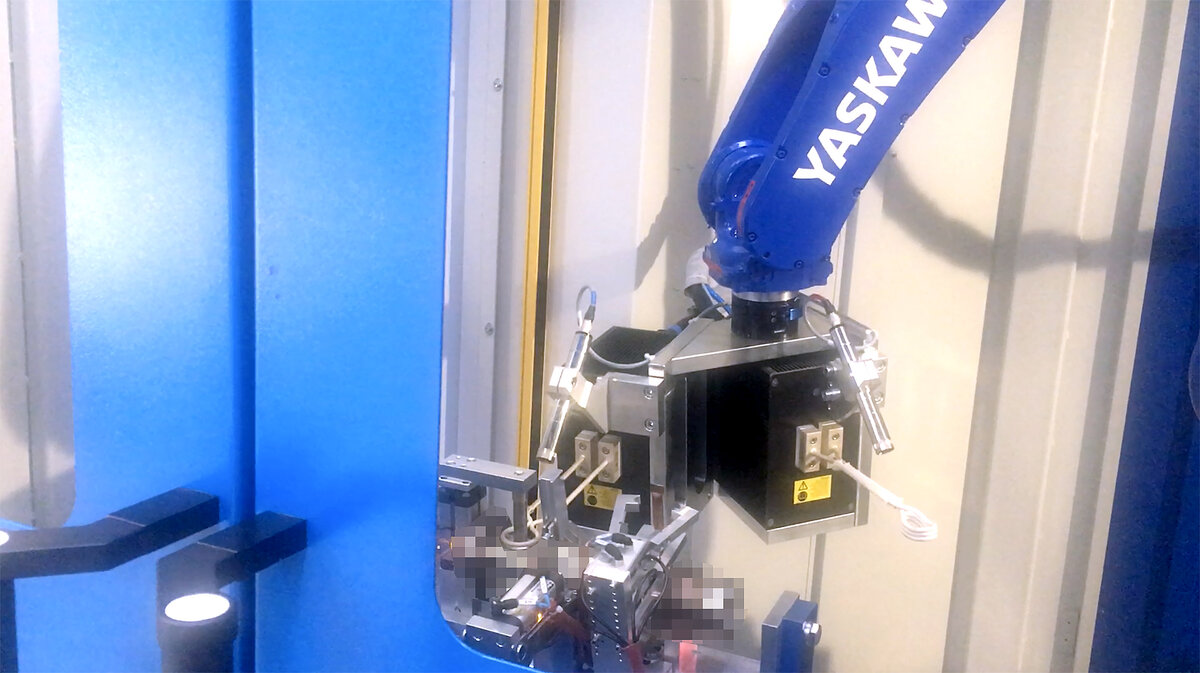