Met meer dan 100 jaar toegewijd aan technische vooruitgang zijn wij een toonaangevende fabrikant op het gebied van frequentieregelaars, servoaandrijvingen, besturingstechnologie en robotica.
Servotechnologie voor betere prestaties
Stoelwielen beschermen bespaart verpakking
Besparing op verpakking is een veelbesproken onderwerp geworden, zelfs voor grote voorwerpen zoals bureaustoelen. Om ervoor te zorgen dat deze goederen onbeschadigd bij de klant aankomen, kunnen de wielen worden beschermd met plastic doppen. Het is dan voldoende om de stoelen tijdens het transport gewoon af te dekken, zodat er geen omslachtig karton nodig is. Stoel- en meubelwielspecialist Gross+Froelich vertrouwt op moderne automatiseringstechnologie om de ringvormige beschermkappen aan te brengen. De servodrives uit de Sigma-7 serie en controls uit de SLIO serie van Yaskawa spelen hierbij een sleutelrol.
Alles wat wielen heeft, hoeft niet te worden gedragen. Dat betekent natuurlijk niet dat uw typische bureaustoel helemaal naar de klant wordt geduwd, maar de wielen van de stoel kunnen zeker worden gebruikt om ze van de vrachtwagen naar de parkeerplaats naar het bureau op kantoor te vervoeren. Om ervoor te zorgen dat ze daar zonder krassen aankomen, moeten de wielen echter worden beschermd. Plastic doppen zijn hiervoor een goede oplossing. Na het transport zijn ze gemakkelijk te verwijderen en te recyclen. Maar hoe worden de beschermdoppen op de stoelwielen gezet?
- Toepassingen
- Picking | packing
- Montage
- Klant
- Gross+Froelich GmbH & Co. KG
- ARAMIS Maschinenbau GmbH & Co. KG
Tot 36.000 doppen per dag
Een stoelwiel bestaat in principe uit twee afzonderlijke wielen, waarbij op elk wiel een dop wordt gedrukt. Dit proces wordt volledig automatisch en met een aanzienlijke snelheid uitgevoerd. Gross+Froelich in het stadje Weil der Stadt in Duitsland gebruikt een machine van ARAMIS Maschinenbau GmbH & Co. KG die nu werkt met cyclustijden van 2,4 seconden na het herontwerp met servotechnologie. Afhankelijk van het model wiel betekent dit dat er in 24 bedrijfsuren tot 36.000 ringvormige beschermkappen volautomatisch op de wielen worden aangebracht, die vervolgens worden verbonden tot het complete wiel verderop in het assemblageproces. Dat zijn ongeveer 10.000 doppen meer dan de machine voor het herontwerp aankon.
Elektrisch vermogen in plaats van pneumatiek
Slechts twee maatregelen waren in principe voldoende om de kortere cyclustijden te bereiken: De capaciteit van de roterende indexeertafel voor de plastic doppen werd verhoogd van vier naar acht houders. Daarnaast werden drie van de pneumatische aandrijvingen in de machine vervangen door zeer dynamische elektrische servoaandrijvingen. Het zou praktisch onmogelijk zijn geweest om de hogere snelheden te bereiken met pneumatische aandrijvingen, omdat de mechanische spanning dan te hoog zou zijn geworden. Bovendien is het persluchtverbruik veel lager, wat een positief effect heeft op de bedrijfskosten.
Voor de elektrische aandrijvingen is gekozen voor de Sigma-7 serie van Yaskawa. Deze hebben zich al bewezen in vele vergelijkbare toepassingen en hebben indruk gemaakt op machinebouwer ARAMIS. Enkele van de bepalende kenmerken van de Sigma-7 serie zijn immers een snelle inbedrijfstelling, een hoge productiecapaciteit en een maximale bedrijfszekerheid. Bovendien hebben de snel reagerende AC-servomotoren extreem compacte afmetingen en draaien ze erg stil. Ze bieden een hoge resolutie (met een geïntegreerde 24-bits absolute encoder) en een hoge dynamiek. Functies zoals trillingsonderdrukking, onderdrukking van machineresonantiefrequenties en een tuningless-functie voor eenvoudig opstarten zijn geïntegreerd in de compacte servoversterkers.
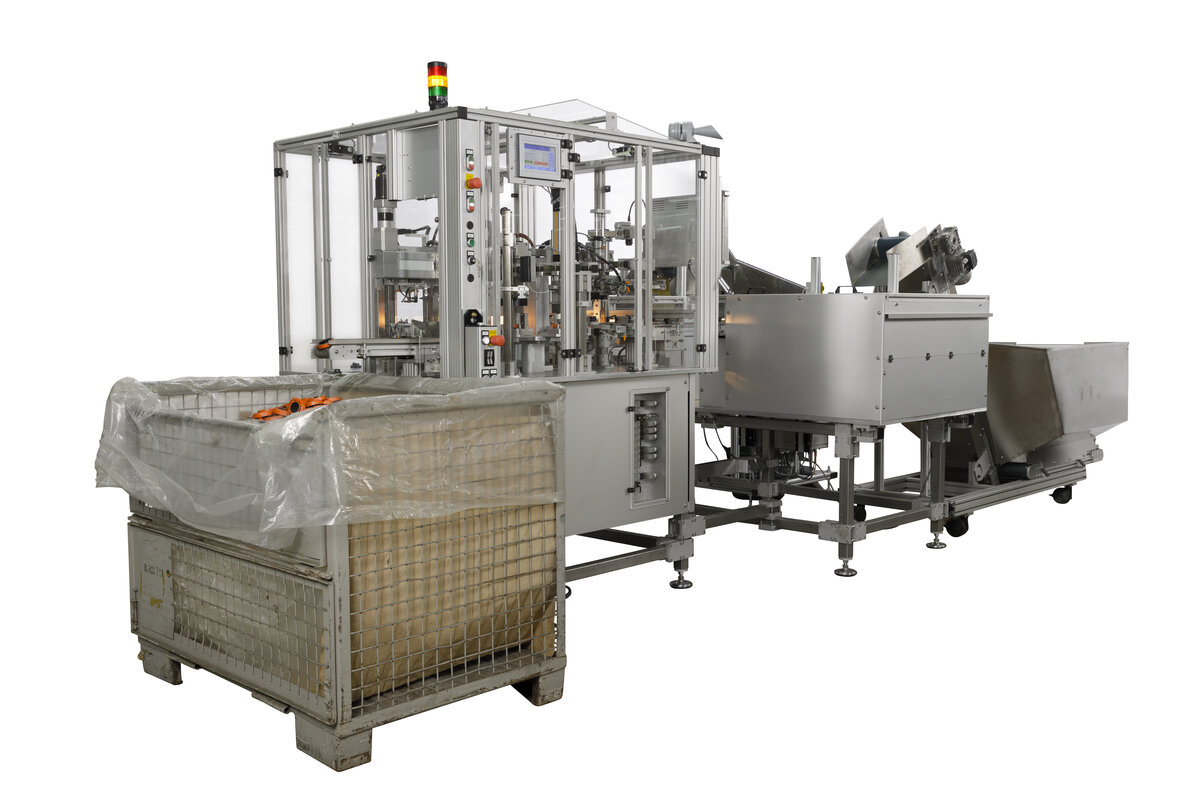
De machinebouwer, zijn elektrische ontwerppartner en de firma Roggenstein Elektronik werkten samen met automatiseringsspecialisten van Yaskawa om de machine om te bouwen voor het aanbrengen van de beschermkappen. In totaal zijn er nu drie 400 V servoassen, elk met 400 W vermogen, in gebruik in de machine: Eén aandrijving is verantwoordelijk voor de horizontale beweging van de aanvoer. Een pneumatische lineaire eenheid met een grijper brengt de plastic kap van de scheidingseenheid naar het nest van de draaitafel. Een elektrische cilinder aangedreven door een tweede servoaandrijving drukt de dop tegen de stoelrol. Een perskrachtsensor detecteert de krachtstoot wanneer ze elkaar raken. Samen met het absolute positiesensorsysteem op de servomotor detecteert deze of het persproces succesvol was. De derde servoaandrijving regelt de horizontale beweging terwijl de afgewerkte onderdelen op de glijgoot worden neergezet, waar de wielen, die nu goed beschermd zijn, naar een traliebox worden getransporteerd en voor verdere assemblage kunnen worden vervoerd.
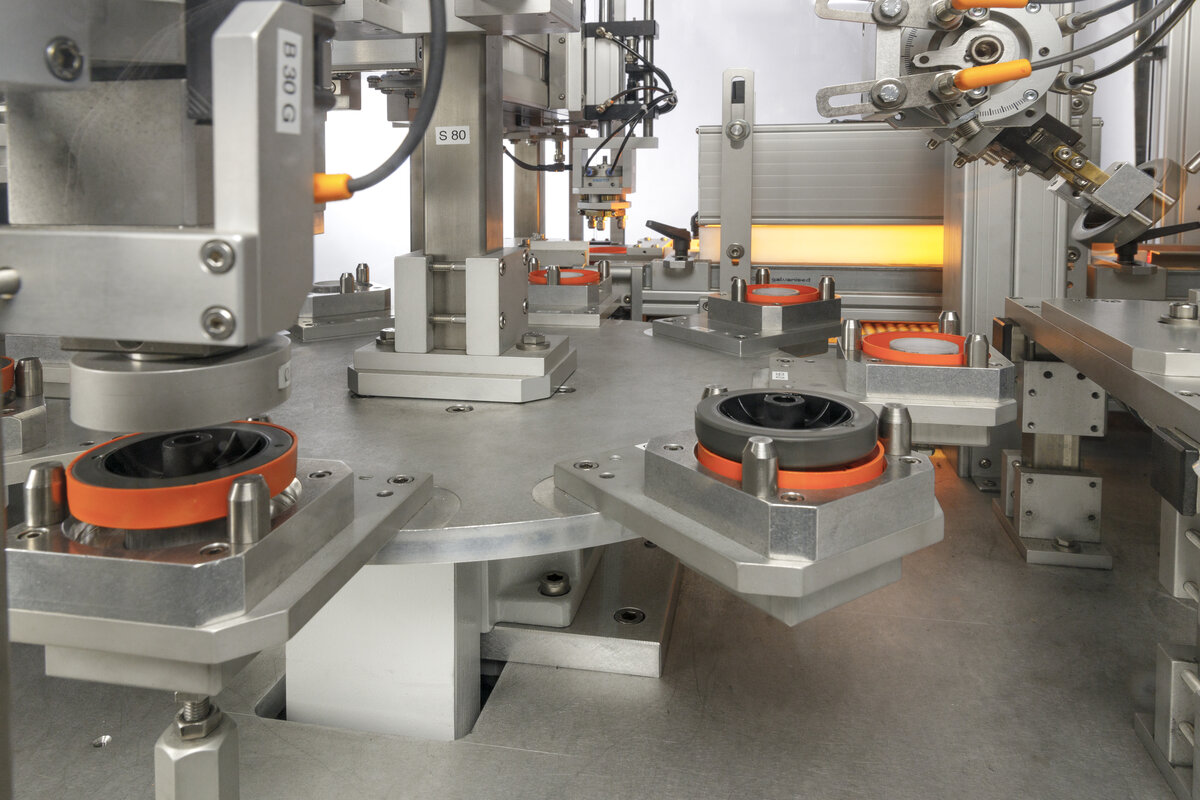
Aandrijvingen, besturing en software uit één hand
De machinebesturing communiceert met de servoassen via Profinet. Deze SLIO-serie besturing, die ook door Yaskawa wordt geleverd, kan eenvoudig in Siemens Step7 worden geprogrammeerd en dankzij de modulaire opbouw effectief aan de toepassing worden aangepast. De benodigde extra I/O-modules konden eenvoudig worden toegevoegd en gekoppeld; in principe zijn ook latere uitbreidingen mogelijk. Extra snelheidsvoordelen worden geleverd door de backplane bus van het I/O-systeem, die werkt met 48 Mbit/s en veldbusonafhankelijk schakelen mogelijk maakt met een timingnauwkeurigheid van +/-1 μs. Korte cyclustijden tijdens de programmaverwerking zorgen voor snelle sequenties. Integratie in de toepassing vergemakkelijkt ook de uitgebreide systeembibliotheek van de controllers, met een groot aantal opgeslagen functies die naar behoefte kunnen worden ingeschakeld. Dit is vooral handig bij het reviseren van oorspronkelijke ontwerpen, vooral als je een bestaande veldbus wilt blijven gebruiken. Profibus is een typisch voorbeeld van zo'n scenario.
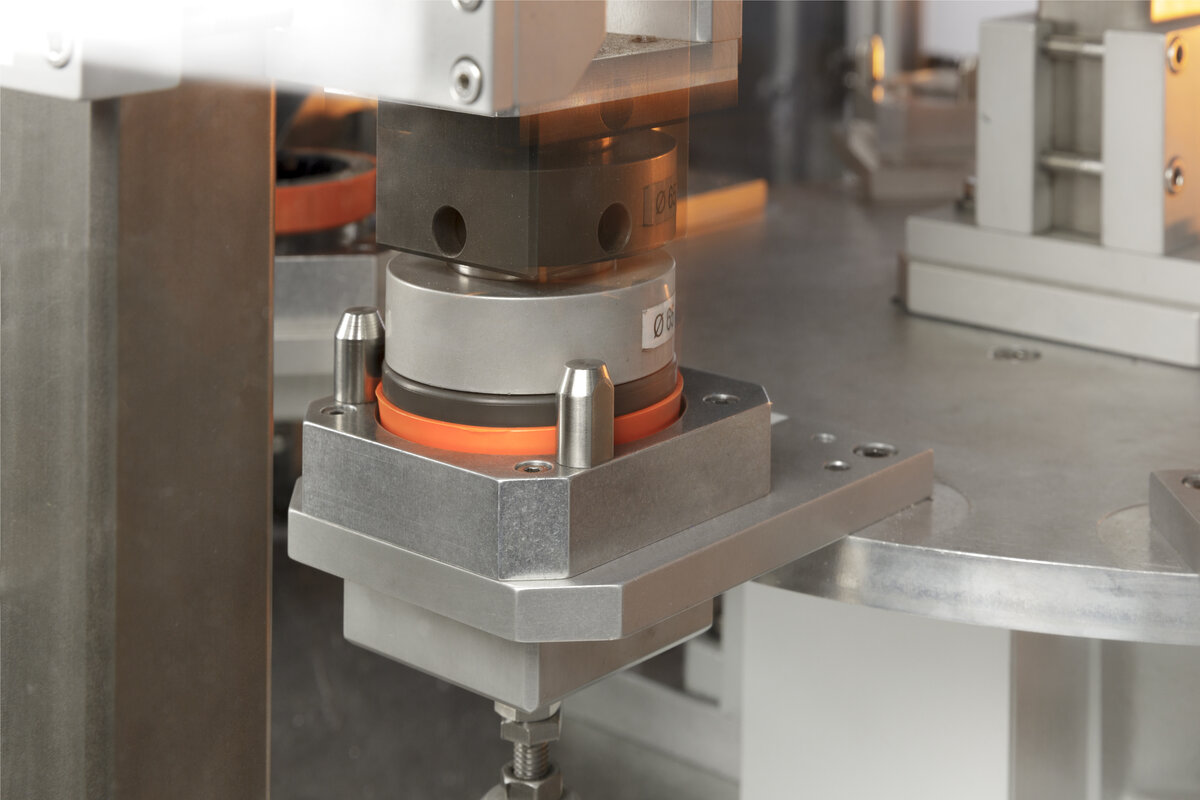
De automatiseringsspecialisten van Yaskawa waren ook een echte hulp voor de machinebouwer en zijn elektrische ontwerppartners toen het ging om softwareaanpassing. Zij assisteerden bijvoorbeeld bij de integratie van pneumatiek, visualisatie en communicatie met het beeldverwerkingssysteem dat Gross+Froelich gebruikt voor kwaliteitsborging. Dankzij dit "single source"-principe was de inbedrijfstelling snel en eenvoudig. De hardware en software zijn perfect op elkaar afgestemd en de machinebouwer had slechts één contactpersoon. Niemand hoefde zich zorgen te maken over interfaceproblemen en de bureaucratie of verloren tijd die daarmee gepaard gaan. De gemoderniseerde machine en de daarin geïnstalleerde componenten hebben zich inmiddels in de praktijk bewezen en ervoor gezorgd dat talloze stoelwielen van beschermkappen zijn voorzien. De zeer dynamische servoassen en krachtige compacte besturing dragen daar dagelijks hun steentje aan bij.