Met meer dan 100 jaar toegewijd aan technische vooruitgang zijn wij een toonaangevende fabrikant op het gebied van frequentieregelaars, servoaandrijvingen, besturingstechnologie en robotica.
Solution for basket loading/unloading cans in autoclave trolleys with Yaskawa robots by DGH for Hijos de Carlos Albo
DGH Robótica, automatización y mantenimiento industrial, S.A. (DGH) is a Spanish company with a national presence and wide international projection, expert in automation and integral maintenance of production processes in all industrial sectors. With more than 40 years of experience, it has installed more than 700 robots in the last 4 years in projects developed in 11 countries in Europe, Africa, Asia and America.
Hijos de Carlos Albo S.L.U. (ALBO) is a Galician canning company with headquarters in Salvaterra de Miño (Pontevedra) and more than 150 years of tradition in the manufacture of canned fish. It currently markets more than 100 references in more than 25 countries. With the new production center set up in the Salvaterra- As Neves Logistics Platform (Pontevedra) at the end of 2022, it has the capacity to process up to 100 tonnes of fish per day and more than 100 million cans per year.
The goal of the DGH proposal is to manage the entire flow of cans coming from the different sealing lines and which have to pass through the autoclaves. In the phase prior to sterilization, the system must place the different types of cans in an orderly manner in the "baskets" or autoclave carts, including a separator between each layer. At the exit of the sterilization process, other equipment must empty the baskets in an orderly manner and send the cans to the subsequent packaging lines.
- Industrieën
- Levensmiddelen & dranken
- Toepassingen
- Handling
- Klant
- DGH Robótica, automatización y mantenimiento industrial, S.A.
- Hijos de Carlos Albo S.L.U.
- Producten
- PL80 - PL serie
- YRC1000 - Controllers
The challenge in managing this flow of cans was the sum of multiple needs:
1. To carry it out in an orderly manner, guaranteeing the traceability of the batches.
2. To carry it out with the greatest possible care for the cans and the packaged product in order to maintain the final quality.
3. To provide the systems with great flexibility in the lines in order to be able to work with different can formats, oval (OL), club (RR), and round (RO), all of them in different sizes.
4. Finally, to tackle the above points according to the work cycles of the sealing or canning systems, in some cases more than 1000 cans per minute.
The solution installed by DGH at the ALBO facilities is composed of:
- For the filling of the carts prior to sterilization in autoclaves, 3 double can crating systems were set up. Each of the systems incorporates a robot that works by filling cans in two lines and taking plastic separators to place between each layer. Empty carts enter from the bottom, with a buffer of empty carts on each of the lines. Each of the double-layer collating systems are independent machines, each with a control cabinet and a screen for monitoring and selecting the work formats. These systems also store job information to allow tracking of their efficiency (OEE).
- For the emptying of the carts at the exit of the autoclaves, 3 systems equivalent to the previous ones were set up to follow a common work philosophy that facilitates their configuration and maintenance. There are 3 double de-cratering systems, where each robot removes layers from two lines of carts and removes the separators, placing them in a common warehouse. As in the previous case, each system has been conceived as an independent machine with individual control and work format selection equipment for each machine.
- For all these actions required by DGH, Yaskawa's Motoman PL80 palletizing robot is the ideal solution that responds specifically to their needs thanks to its ability to easily handle loads of up to 80 kg and exceptionally fast axis speeds. Features that enable optimal, orderly, and highest possible quality production throughput with more than 800 cycles per hour. Its low overall height, robust design, and small footprint allow for greater utilization of the available space in the installation. In addition, the compact, high-performance YRC1000 controller that runs the Motoman PL series robots is essential thanks to its wide range of track planning and communication functions.
The benefits obtained by the client are based on the challenges initially defined. Working at high speed, with the flexibility to incorporate different formats, care of the product handled with control of the manufacturing batches.
In addition, work has been done on the simplicity of handling the installations so that the same people who previously worked in a manual process, with customized training, are now able to operate installations with robots in a simple and safe manner.
Without disclosing data that would compromise due confidentiality, we can assure that the objectives and benefits defined above have been achieved with measured machine availability rates above 90%.
This solution can be used or adapted in similar processes in the canned vegetable, jam, etc. industries, or with other types of packaging, glass jars, pouches, and the like.
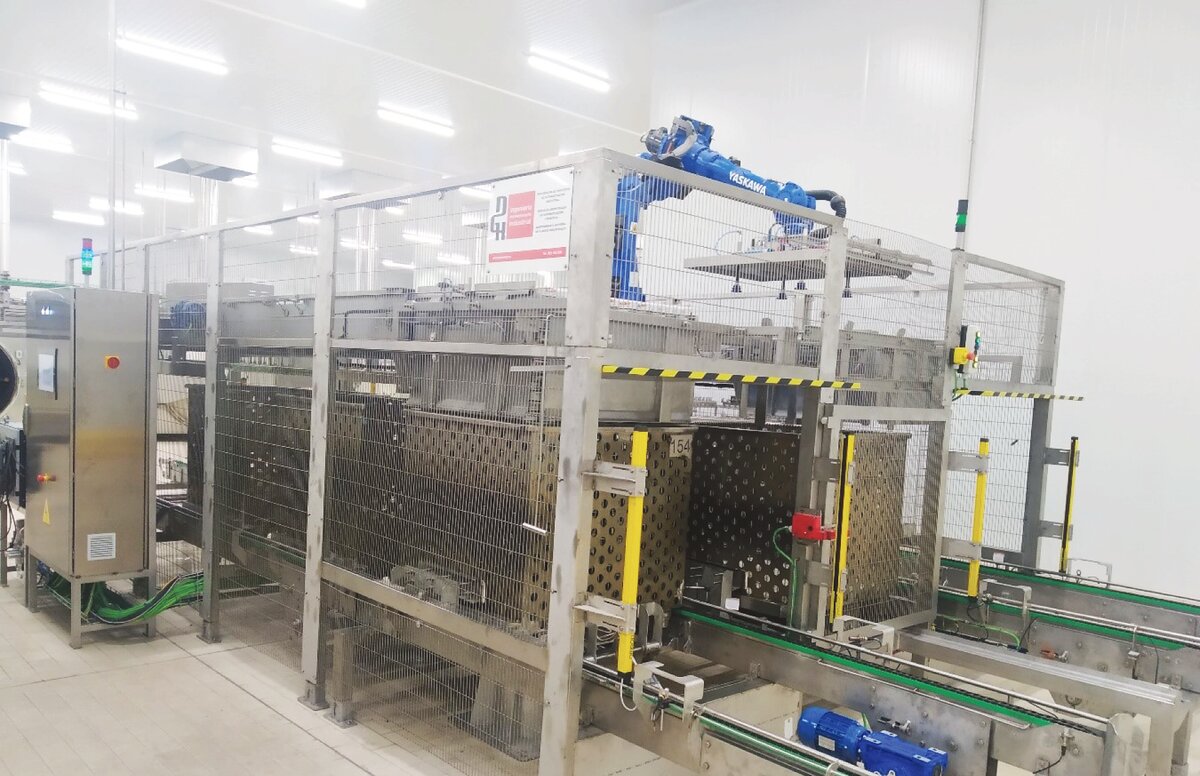

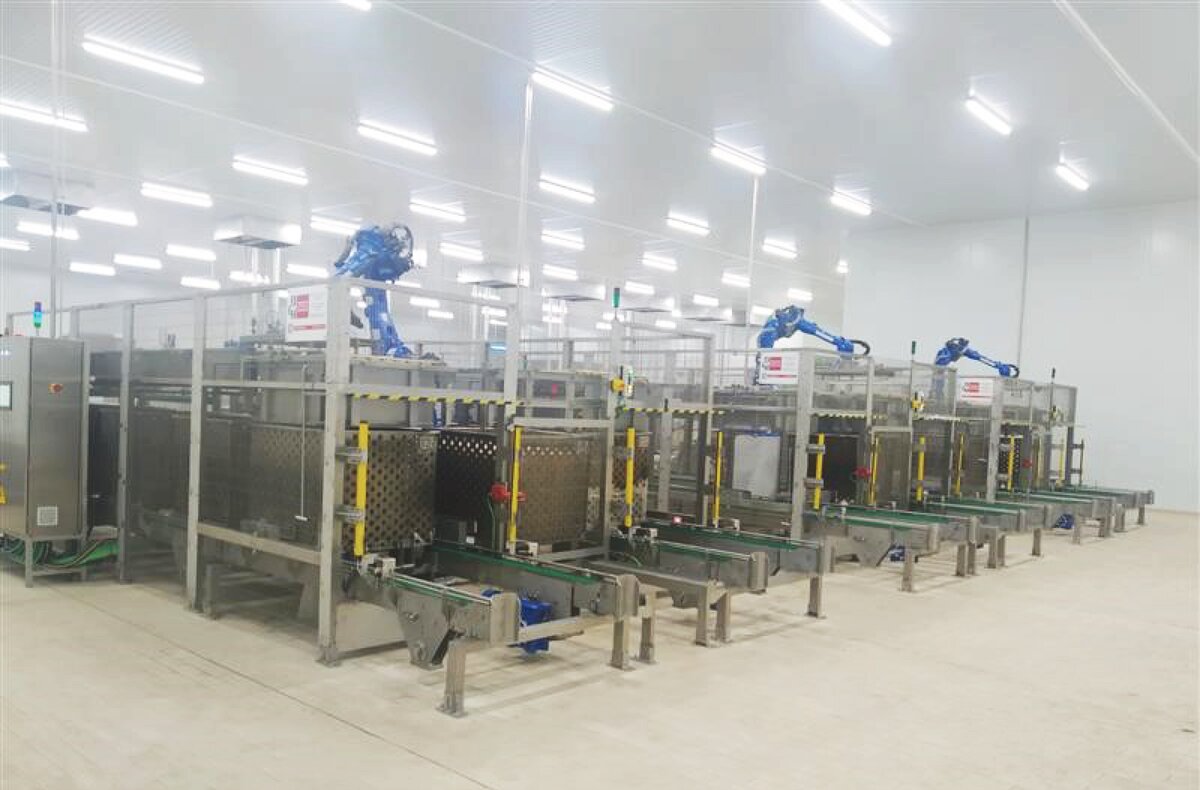
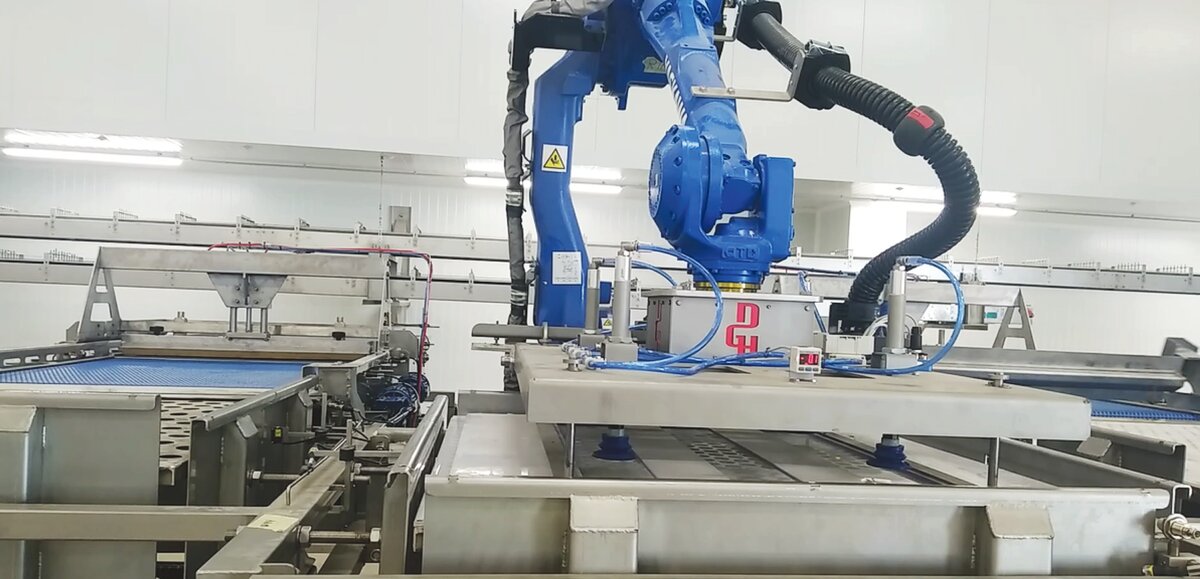